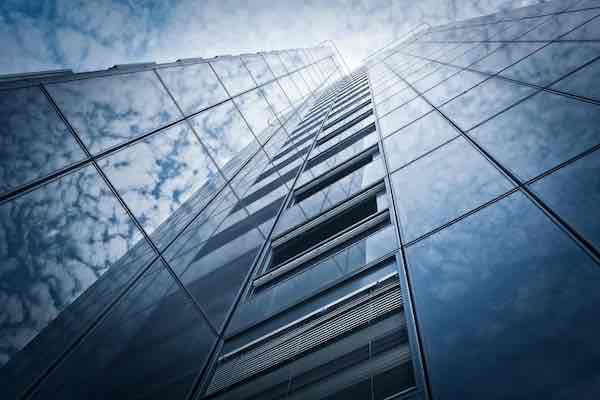
When it comes to life safety systems in buildings smoke control plays a key role, keeping escape and access routes free of smoke in order to facilitate fire-fighting operations and enabling safe evacuation of buildings during a fire.
Compliance
Since 2013, when the Construction Products Regulations (CPR) mandated the CE marking of all products used within the construction industry, smoke ventilation products and systems used in any part of the UK should conform to applicable standards within the EN12101 suite. Any product that does not comply with the relevant standard cannot legitimately receive a CE mark or the more recently introduced UKCA mark.
The key standards for the vast majority of smoke control products are EN12101-2, 3, 6, 7, 8 and 10 but we are going to take a closer look at EN12101-2 and its test requirements.
EN12101-2 applies to natural smoke and heat exhaust ventilators (NSHEV) operating as part of smoke and heat exhaust ventilation systems (SHEVS).
In a fire, SHEVS create and maintain a smoke-free layer above the floor by removing smoke. They also serve simultaneously to exhaust hot gases released by a fire in the developing stages. It is therefore essential that these life safety systems can be called upon to operate reliably and in the intended manner during a fire emergency.
The EN12101-2 test criteria is stringent and clearly states that the vent and actuator must be tested together to all specifications and that test should be undertaken at an accredited facility. Simply fitting an actuator to a vent or window does not provide a compliant solution and compromises the effectiveness of the entire life safety system. Test results are subsequently declared via a certification process, proving compliance to the CPR.
Certification
Since the introduction of the CPR, the industry has made great strides in ensuring that fully compliant products and systems are used in the installation of smoke control life safety systems, helped in no small part by the establishment of the IFC Certification SDI 19 scheme for companies installing smoke control systems.
This scheme was specifically designed to ensure a suitable and acceptable level of competency with regard to fire strategy verification, system design, installation and commissioning of smoke control systems. It is now a mandatory requirement that Smoke Control Association (SCA) members involved with the installation of smoke ventilation systems must join the IFC SDI 19 Installer scheme.
The SDI 19 installer scheme classifications are as follows:
Category 1 – Smoke control service and maintenance companies who carry out small refurbishments, remedials and replacement projects and install EN12101 compliant products and controls only.
Category 2 – Smoke control companies installing ADB code compliant staircase AOV systems, corridor smoke ventilation systems and simple natural smoke ventilation systems with no significant design input or CFD verification required.
Category 3 – Smoke control companies installing natural smoke shafts, smoke damper installations, natural smoke ventilation for atria, retail, commercial and industrial.
Category 4 – Smoke control companies installing complex smoke control systems including mechanical smoke shafts, pressurisation systems, mechanical smoke ventilation, car park smoke control systems and custodial smoke control systems.
Positive change
At this point it’s important to note that whilst the CPR and SDI 19 installer scheme have undoubtedly helped to bring about positive change, there are still areas of the country where there is work to be done. The impetus is then on individual nations and regions to drive home the message that standards apply throughout the whole of the UK.
Proof of compliance in the form of a Declaration of Performance (DoP) is therefore vital to ensure that any life safety product or system is fully compliant in line with UK law. The DoP can be requested by the client, contractor or approved inspectors. Reputable manufacturers will be able to provide a DoP to prove that their products have been independently tested and certified. Put simply, where a harmonised standard exists, products lacking a valid DoP are not compliant and should not be on the market. A full audit of the supply chain carried out by a third party/notified body will add an additional layer of confidence, ensuring that all elements will be delivered in accordance with the relevant laws, regulations and industry standards.
Following the Grenfell Tower fire, Dame Judith Hackitt’s Independent Review of Building Regulations and Fire Safety discussed the transition towards a clearer, more transparent and more effective specification and testing regime of construction products and recommended that the testing of products that are critical to the safety of high-risk residential buildings should be subject to independent third-party certification. Organisations the length and breadth of the country now need to understand their obligations to safety when bringing life critical products to market – non-compliance may be policed by Approved Inspectors, Building Control Officers and the new Office of Product Safety Standards but overall responsibility remains with the company bringing the product to market.
Schemes such as SDI 19 are in place to help raise the bar on competency standards and drive home the message of compliance, offering a reassurance that a life safety system is fit for purpose – it’s time for the whole of the UK to come together and make it clear that anything less than this will no longer be accepted.